Introduction
In the realm of modern engineering, nitinol spring actuators have emerged as a fascinating innovation, combining the unique properties of shape memory alloys (SMAs) with practical applications in various industries. These remarkable devices leverage the shape memory effect to create movement and force in a compact and efficient manner. As we delve into the intricacies of nitinol wire and its role in actuator springs, we will uncover how this technology is revolutionizing designs across multiple sectors.
Understanding Nitinol Spring Actuators
Nitinol spring actuators are specialized devices that utilize nitinol wire to achieve precise motion through thermal activation. When heated, the shape memory alloy nitinol undergoes a transformation, allowing it to return to its predetermined shape and exert force—essentially mimicking the function of traditional linear actuators but with added benefits. By understanding how these SMA actuators work, we can appreciate their potential to enhance mechanical systems with improved efficiency and responsiveness.
The Science Behind Shape Memory Alloys
The science behind shape memory alloys is rooted in their ability to remember an original shape after deformation when subjected to specific temperature conditions. Nitinol, a nickel-titanium alloy, exhibits this unique behavior due to its crystalline structure changes that occur at different temperatures. This property not only makes nitinol spring actuators highly effective but also opens doors for innovative designs that were previously unimaginable with conventional materials.
Applications of Nitinol in Actuator Design
Nitinol's versatility has led to its adoption across various industries where actuator design plays a critical role. From medical devices like stents that expand within the body to aerospace applications where lightweight materials are crucial for performance, the use of SMA wire is transforming how engineers approach design challenges. As we explore these applications further, it becomes clear that nitinol spring actuators are not just a passing trend; they represent a significant leap forward in actuator technology.
What is a Nitinol Spring Actuator?
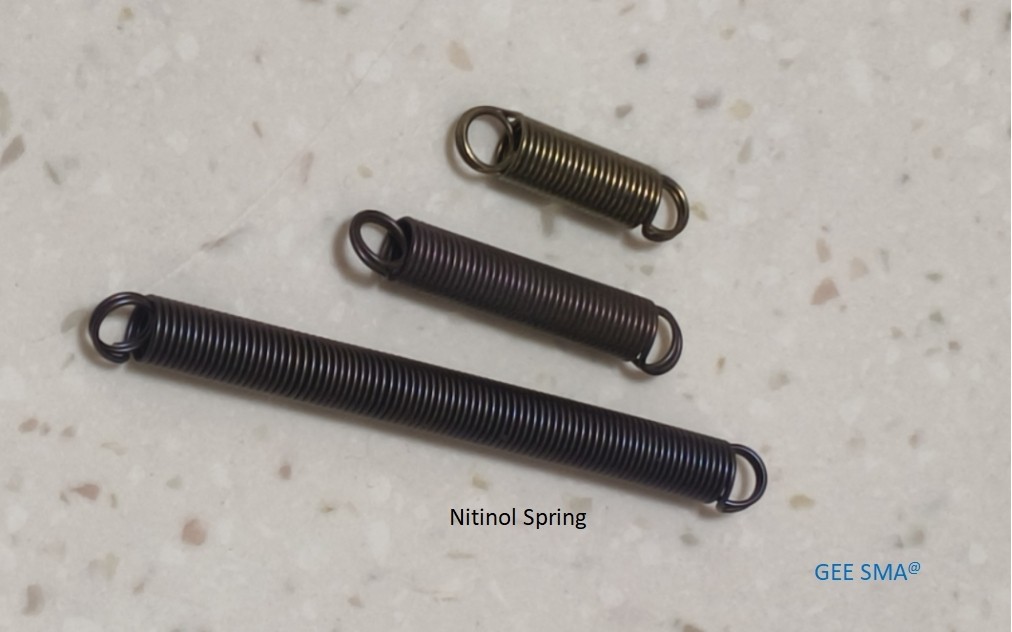
Nitinol spring actuators are fascinating devices that harness the unique properties of shape memory alloys (SMAs), specifically nitinol, to create movement in response to temperature changes. These actuator springs work by exploiting the shape memory effect, allowing them to return to a predetermined shape when heated. The combination of nitinol wire and innovative design leads to efficient and reliable actuation in various applications.
Definition and Mechanism
A nitinol spring actuator is essentially a type of actuator that utilizes nitinol wire, which can change its shape based on temperature variations. When heated above a certain threshold, the nitinol wire transforms into its active state, enabling it to contract and perform mechanical work. This mechanism provides an elegant solution for motion control in systems where traditional linear actuators might fall short.
The operation of a shape memory alloy actuator relies on two distinct phases: the martensite phase at lower temperatures and the austenite phase at higher temperatures. In practical terms, this means that when you cool down the nitinol wire, it can be deformed easily but will return to its original form once heated again. This remarkable property allows for precise control over movement with minimal energy consumption.
Comparison with Traditional Linear Actuators
When comparing nitinol spring actuators to traditional linear actuators, several key differences emerge that highlight their unique advantages. Traditional linear actuators often rely on electric motors or hydraulic systems for movement, which can be bulky and require significant power input. In contrast, SMA actuators like those made from nitinol wire are compact and lightweight while providing similar or even superior performance.
Moreover, traditional linear actuators typically have many moving parts that can wear out over time; however, nitinol spring actuators have fewer components due to their simple design based on the properties of shape memory alloys. This not only enhances reliability but also reduces maintenance needs significantly. Additionally, since they operate silently without motors or pumps, these actuator springs offer a level of discretion that's hard to match.
Advantages of Using Nitinol Wire
Using nitinol wire in actuator design brings numerous benefits that make it an attractive choice across various industries. One major advantage is its ability to generate high forces relative to its size; this allows for compact designs without sacrificing performance capabilities in applications such as robotics or medical devices utilizing SMA technology.
Another significant benefit lies in energy efficiency; because these shape memory alloy nitinol components only consume power during activation—unlike traditional systems that may require continuous energy input—they help reduce overall operational costs while maintaining performance standards. Furthermore, their resilience against fatigue and corrosion makes them ideal for long-term use in challenging environments.
In summary, the integration of nitinol wire into actuator springs opens up new avenues for innovation across multiple sectors by providing efficient solutions with enhanced reliability and reduced maintenance requirements.
Design Principles of Nitinol Actuators
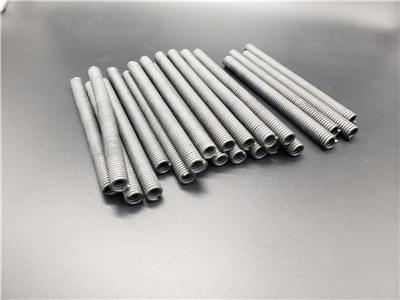
Designing a nitinol spring actuator involves a careful balance of engineering principles and innovative materials science. As these actuators rely on the unique properties of shape memory alloys (SMAs), understanding their behavior under different conditions is crucial. This section will explore key design considerations, the pivotal role of the shape memory effect, and the customization options available for actuator springs.
Key Design Considerations
When designing a nitinol spring actuator, several factors must be taken into account to ensure optimal performance. One primary consideration is the operating temperature range; since nitinol wire exhibits its shape memory effect within specific thermal limits, engineers need to select appropriate temperatures for activation. Additionally, load capacity and stroke length are critical parameters that determine how effectively the actuator can perform its intended task compared to traditional linear actuators.
Another important aspect is the fatigue resistance of the nitinol wire used in actuator springs. Given that these SMA actuators undergo repeated cycles of deformation and recovery, ensuring durability over time is paramount for reliable operation. Lastly, integration with control systems must be considered; effective communication between sensors and actuators can enhance overall system performance and efficiency.
Role of Shape Memory Effect
The shape memory effect is at the heart of every nitinol spring actuator's functionality, allowing these devices to return to their original shapes after being deformed when subjected to heat. This phenomenon occurs due to phase transformations within the shape memory alloy nitinol, which transitions between austenite (the high-temperature phase) and martensite (the low-temperature phase). By harnessing this property, engineers can create highly efficient SMA actuators that respond dynamically to thermal stimuli.
Moreover, this effect enables precise control over movement in applications ranging from medical devices to aerospace innovations. The ability to program specific temperature thresholds means that a single nitinol wire can be tailored for various tasks without extensive mechanical components or complex designs typical in traditional linear actuators. This not only simplifies construction but also reduces weight—a crucial factor in many high-tech applications.
Customization Options for Actuator Springs
Customization options for actuator springs using nitinol wire offer tremendous versatility in design and application suitability. Engineers can manipulate various parameters such as wire diameter, coil geometry, and heat treatment processes to achieve desired characteristics like stiffness or response time in their SMA actuators. This level of customization allows designers to fine-tune performance based on specific operational requirements or constraints within their projects.
Additionally, surface treatments can enhance corrosion resistance or improve friction properties when integrating with other components—further extending the lifespan of these innovative devices while maintaining efficiency during operation. With advancements in manufacturing techniques allowing for precise fabrication methods like 3D printing or laser cutting, creating bespoke shapes tailored specifically for unique applications has never been easier.
In summary, understanding design principles surrounding nitinol spring actuators—such as key considerations related to temperature ranges and fatigue resistance—combined with leveraging the remarkable shape memory effect allows engineers greater flexibility in creating efficient solutions across multiple industries.
Manufacturing Process of Nitinol Components
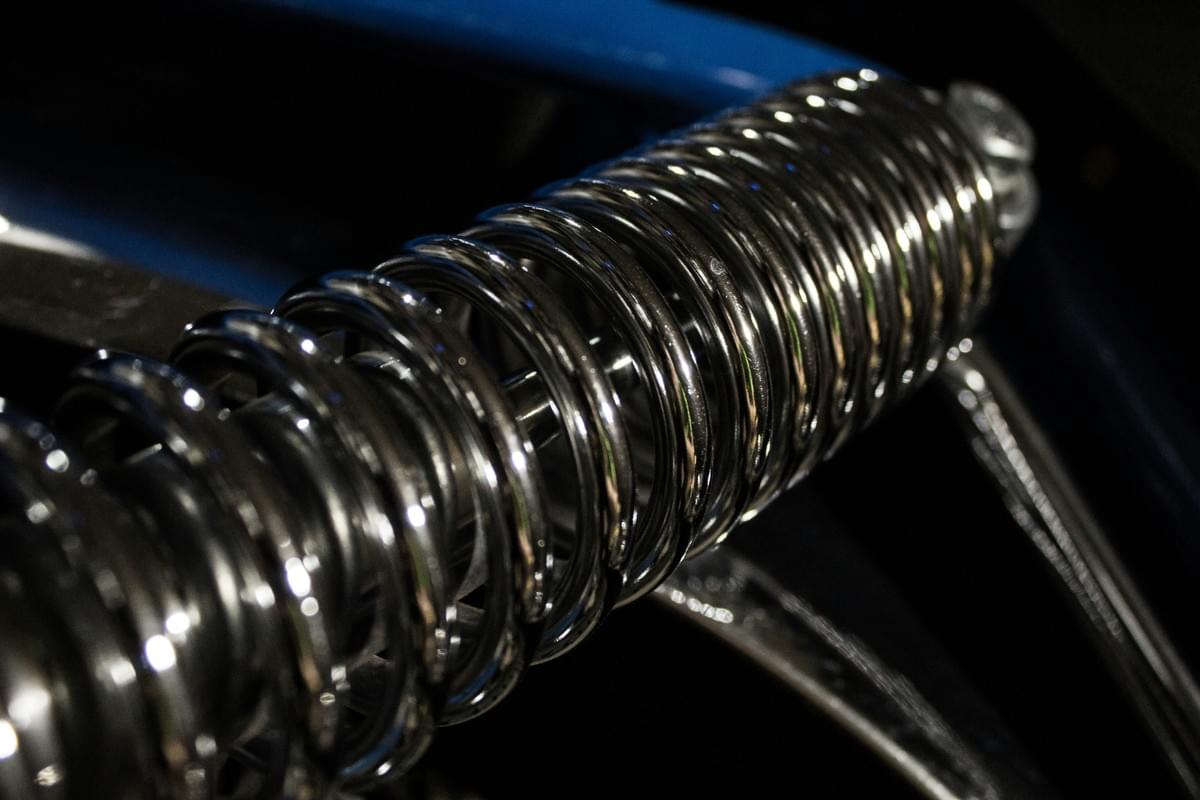
The manufacturing process of nitinol components is a fascinating journey that transforms raw materials into highly functional products, particularly nitinol spring actuators. These components are crafted with precision and care, ensuring that the unique properties of shape memory alloys (SMAs) are preserved throughout production. Understanding the techniques and quality control measures involved is crucial for anyone looking to utilize nitinol wire in actuator designs.
Techniques Used in Production
Producing nitinol spring actuators involves several sophisticated techniques that harness the unique characteristics of shape memory alloy nitinol. Initially, the process begins with the careful selection of raw materials, where high-purity nickel-titanium alloys are chosen to ensure optimal performance. The manufacturing methods include processes such as hot working, cold working, and thermal treatment—all designed to enhance the shape memory effect inherent in SMA actuators.
Once shaped into wires or springs, these components undergo heat treatment to lock in their desired configurations. This step is critical as it determines how effectively the nitinol wire will respond to temperature changes during operation. Advanced techniques like laser cutting and CNC machining further refine these actuator springs, allowing for precise dimensions tailored to specific applications.
Quality Control Measures
Quality control is paramount when it comes to producing reliable nitinol components for linear actuators or other applications. Rigorous testing protocols are implemented at various stages of production to ensure that each batch meets strict performance standards associated with shape memory alloy actuators. This includes mechanical testing for fatigue resistance and thermal cycling tests that assess how well the actuator springs perform under varying temperatures.
To maintain consistency and reliability, manufacturers often employ statistical process control (SPC) techniques throughout production processes. This helps identify any deviations from desired specifications early on, allowing for timely adjustments before products reach consumers or industries relying on these advanced materials. Ultimately, effective quality control ensures that every piece of SMA wire meets expectations—whether it's used in aerospace innovations or medical devices.
Case Study: GEE SMA's Innovative Processes
GEE SMA stands out as a pioneer in the field of manufacturing nitinol components through innovative processes tailored specifically for shape memory alloy applications. Their approach combines cutting-edge technology with extensive research into material science, leading them to develop proprietary methods for producing high-performance nitinol spring actuators consistently. By embracing automation alongside traditional craftsmanship, GEE SMA has streamlined their operations while maintaining exceptional quality.
One notable aspect of GEE SMA's production is their commitment to sustainability practices within their manufacturing processes—reducing waste and energy consumption without compromising on output quality or performance metrics associated with SMA actuators. They have also established partnerships with industry leaders across various sectors including automotive and aerospace—showcasing their versatility in delivering customized solutions using advanced nitinol wire technologies.
In conclusion, understanding the intricate manufacturing processes behind nitinol components provides valuable insights into how these remarkable materials can be harnessed effectively across diverse applications—from actuator springs in robotics to life-saving medical devices.
Applications Across Industries
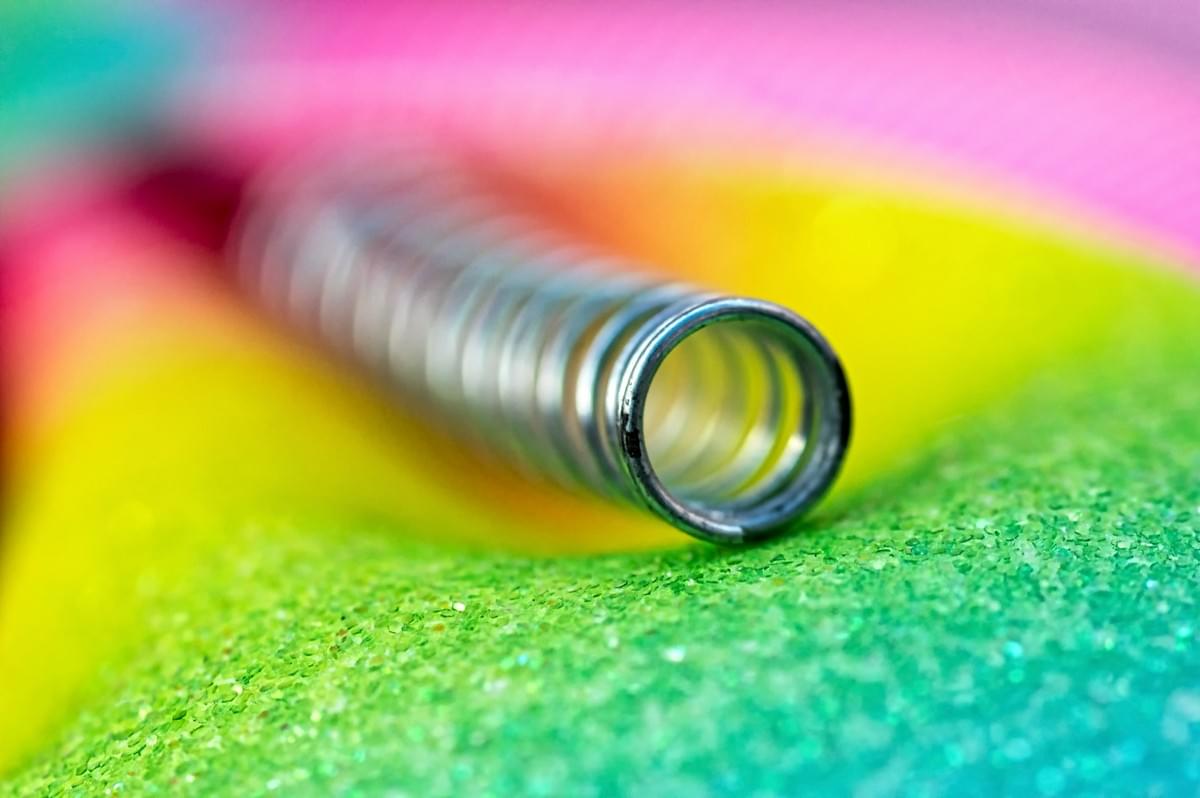
Nitinol spring actuators are revolutionizing various industries with their unique properties and capabilities. From medical devices to aerospace innovations, the versatility of shape memory alloys is paving the way for advanced solutions that were previously unimaginable. This section explores how nitinol wire is utilized across different sectors, highlighting its benefits and applications.
Medical Devices Utilizing Nitinol Actuators
In the medical field, nitinol actuators have become indispensable due to their biocompatibility and reliability. Surgical instruments, such as stents and guidewires, leverage the shape memory effect of nitinol wire to adapt to complex anatomical structures while providing superior performance. The inherent flexibility and strength of these actuator springs allow for minimally invasive procedures, significantly enhancing patient outcomes.
Moreover, SMA actuators are increasingly employed in robotic-assisted surgeries where precision is paramount. The ability of shape memory alloy actuators to return to a predetermined shape upon heating makes them ideal for applications requiring exact movements and adjustments. As technology advances, we can expect even more innovative uses for nitinol in medical devices that prioritize safety and efficiency.
Aerospace Innovations with Shape Memory Alloys
The aerospace industry is also reaping the rewards of incorporating nitinol spring actuators into aircraft designs. These SMA components can withstand extreme temperatures while maintaining functionality, making them perfect for critical systems like wing morphing technologies or deployable landing gear mechanisms. The lightweight nature of nitinol wire contributes to overall fuel efficiency—an essential factor in modern aviation.
Additionally, the adaptability of shape memory alloy actuators allows for dynamic responses during flight operations, enhancing control surfaces' effectiveness under varying conditions. Engineers are continuously exploring new ways to integrate these innovative materials into aerospace applications that demand both reliability and performance under pressure. With ongoing research and development efforts, we anticipate a surge in aerospace innovations utilizing these remarkable actuator springs.
Automotive Applications and Benefits
In the automotive sector, nitinol's unique properties are transforming vehicle design and functionality through advanced actuation systems. Nitinol spring actuators are being employed in various applications ranging from active suspension systems to adaptive seating configurations that enhance comfort during travel. By utilizing SMA wire technology, manufacturers can create more responsive systems that improve overall driving experiences.
Furthermore, these actuator springs contribute significantly to weight reduction—a critical aspect as electric vehicles gain popularity worldwide. Lighter vehicles not only consume less energy but also exhibit better handling characteristics on the road. As automakers continue embracing sustainable practices alongside cutting-edge technologies like shape memory alloys, we can expect a brighter future filled with smarter automotive solutions powered by nitinol.
Future Trends in Nitinol Spring Actuator Design
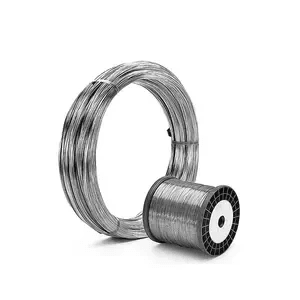
The landscape of nitinol spring actuators is evolving rapidly, driven by innovations in shape memory alloy (SMA) technologies and a growing emphasis on sustainability. As industries increasingly seek efficient and adaptable solutions, the role of nitinol wire in actuator design is becoming more prominent. With advancements in materials science and engineering techniques, the future looks bright for shape memory alloy actuators.
Advancements in SMA Technologies
Recent advancements in SMA technologies are pushing the boundaries of what a nitinol spring actuator can achieve. Researchers are exploring new compositions and processing methods to enhance the performance characteristics of SMA wire, enabling it to operate at higher temperatures and under greater loads. These innovations not only improve the efficiency of linear actuators but also expand their application range across various sectors.
Moreover, smart integration with IoT devices is on the rise, allowing for real-time monitoring and control of shape memory alloy actuators. This interconnectedness will lead to more responsive systems that can adapt to changing conditions instantly. By leveraging these technological advancements, manufacturers can create more versatile actuator springs that meet diverse industry needs.
Sustainable Practices in Production
Sustainability is no longer just a buzzword; it's becoming an essential aspect of manufacturing processes across all industries, including those producing nitinol spring actuators. The push towards sustainable practices involves reducing waste during production and utilizing environmentally friendly materials wherever possible. Companies are beginning to adopt recycling methods for used SMA wire, which not only cuts costs but also minimizes environmental impact.
Furthermore, energy-efficient manufacturing techniques are being prioritized to reduce carbon footprints associated with producing shape memory alloy components. This focus on sustainability ensures that as demand for nitinol actuators grows, it does so without compromising environmental integrity or depleting natural resources. Emphasizing sustainable practices will likely become a key differentiator among manufacturers of SMA actuators.
Predictions for Market Growth
The market for nitinol spring actuators is poised for significant growth over the coming years as industries recognize their unique advantages over traditional linear actuators. Analysts predict an increase in demand driven by advancements in medical devices, aerospace applications, and automotive innovations involving shape memory alloys. As companies continue to invest in research and development around SMA technology, we can expect even broader adoption across various fields.
Moreover, as awareness about the benefits of using nitinol wire increases—such as its lightweight nature and high fatigue resistance—more sectors will explore its potential applications beyond current uses. The versatility of shape memory alloy actuators positions them well within emerging markets focused on automation and robotics where precise actuation is critical. Overall, this trend indicates a robust future ahead for both manufacturers and users involved with nitinol spring actuator technology.
Conclusion
In wrapping up our exploration of nitinol spring actuators, it's clear that these innovative devices are revolutionizing the way we think about motion and control. The unique properties of nitinol wire, particularly its shape memory effect, allow for remarkable flexibility and efficiency in actuator springs compared to traditional linear actuators. As industries continue to adopt these advanced technologies, the benefits of using shape memory alloy actuators become increasingly apparent.
Recap of Nitinol Spring Actuator Benefits
Nitinol spring actuators offer a plethora of advantages that make them stand out in the world of automation and control systems. Their ability to return to a predetermined shape when heated allows for precise movement without the need for complex mechanical components, making them lighter and more compact than conventional linear actuators. Additionally, the durability and fatigue resistance of nitinol wire ensure a longer lifespan for actuator springs, reducing maintenance costs and enhancing reliability across various applications.
The Role of GEE SMA in Advancements
GEE SMA has been at the forefront of advancing nitinol technology, pushing the boundaries of what's possible with shape memory alloys. Their commitment to innovation has led to improved manufacturing processes that enhance the performance and customization options available for SMA actuators. By focusing on quality control measures and cutting-edge production techniques, GEE SMA is not only elevating their own products but also setting new standards within the industry for nitinol spring actuator design.
Final Thoughts on Shape Memory Alloys
As we look toward the future, it’s evident that shape memory alloys like nitinol will continue to play a pivotal role in engineering advancements across multiple sectors. From medical devices that require precision actuation to aerospace applications where weight savings are critical, SMA wire technology is poised for significant growth and innovation. Embracing these materials will not only lead to enhanced product performance but also foster sustainable practices within manufacturing—an exciting prospect indeed!