Introduction
Nitinol, a fascinating alloy of nickel and titanium, has captured the attention of engineers and innovators alike due to its remarkable properties and diverse applications. From medical devices to robotics, Nitinol springs play a crucial role in modern technology, showcasing their unique ability to revert to a predetermined shape when heated. But what exactly is a Nitinol spring? This introduction will explore the essence of Nitinol, the science behind shape memory alloys, and how temperature characteristics influence the performance of these incredible materials.
What is Nitinol and Its Applications
At its core, Nitinol is not just any ordinary metal; it’s a shape memory alloy that can remember its original form after being deformed. This remarkable property makes it invaluable in various applications ranging from stents in medical procedures to actuators in robotics. The versatility of Nitinol springs allows them to be used effectively across sectors like aerospace, automotive, and even consumer electronics—demonstrating that this alloy is indeed special.
Shape Memory Alloys Explained
Shape memory alloys (SMAs) are materials that can undergo significant deformation but return to their original shape when exposed to certain temperatures. The magic behind SMAs lies in their unique phase transformation process; when heated above a specific temperature threshold, they transition from a martensitic phase (deformed) back to an austenitic phase (original form). Understanding what makes these alloys tick helps us appreciate why Nitinol springs are so widely utilized; they’re not just flexible—they’re smart!
Nitinol Spring Temperature Characteristics
When discussing the functionality of a Nitinol spring, one question often arises: what is the temperature of a Nitinol spring? The answer lies within specific operating ranges that define how these springs behave under different thermal conditions. Typically, the transformation temperatures can be tailored during manufacturing processes, allowing for customized performance based on application needs—whether that's maintaining stiffness at room temperature or becoming pliable at higher temperatures. Understanding these characteristics is essential for anyone looking to harness the full potential of this extraordinary material.
Understanding Nitinol Springs
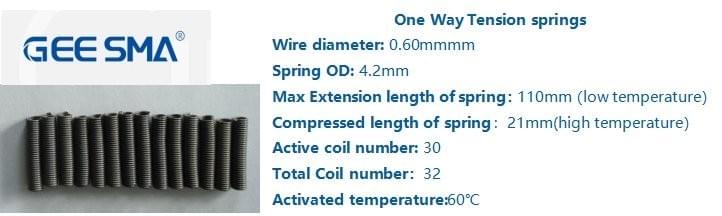
Nitinol springs are a fascinating application of shape memory alloy technology, specifically made from Nitinol, a nickel-titanium alloy known for its unique ability to return to a predetermined shape when heated. These springs can undergo significant deformation and still revert to their original form when exposed to specific temperatures. This remarkable property makes Nitinol springs not just functional but also a source of intrigue in various industries.
What is a Nitinol spring?
So, what is a Nitinol spring? Simply put, it's a spring crafted from the shape memory alloy Nitinol that can change its shape based on temperature variations. When cooled below its transformation temperature, the spring can be easily deformed; however, once it heats up again—typically around body temperature—it returns to its original configuration with impressive force. This unique behavior allows for dynamic applications in fields ranging from medical devices to automotive engineering.
Key Properties of Nitinol Springs
Nitinol springs come with an array of key properties that set them apart from traditional metal springs. One standout feature is their ability to exhibit superelasticity at certain temperatures; this means they can stretch significantly without permanent deformation, which is essential for applications requiring flexibility and resilience. Additionally, the temperature sensitivity of these springs leads us back to the question: what is the temperature of a Nitinol spring? The operating range generally lies between 20°C and 100°C (68°F - 212°F), making them suitable for numerous environments.
Applications in Modern Manufacturing
The versatility of Nitinol springs opens doors to various modern manufacturing applications that benefit from their unique characteristics. In the medical field, they are used in stents and guidewires due to their biocompatibility and ability to conform under different conditions while maintaining structure when needed most. Beyond healthcare, industries such as robotics and aerospace leverage these innovative components for actuators and control systems—showing just how special Nitinol truly is.
The Science Behind Nitinol
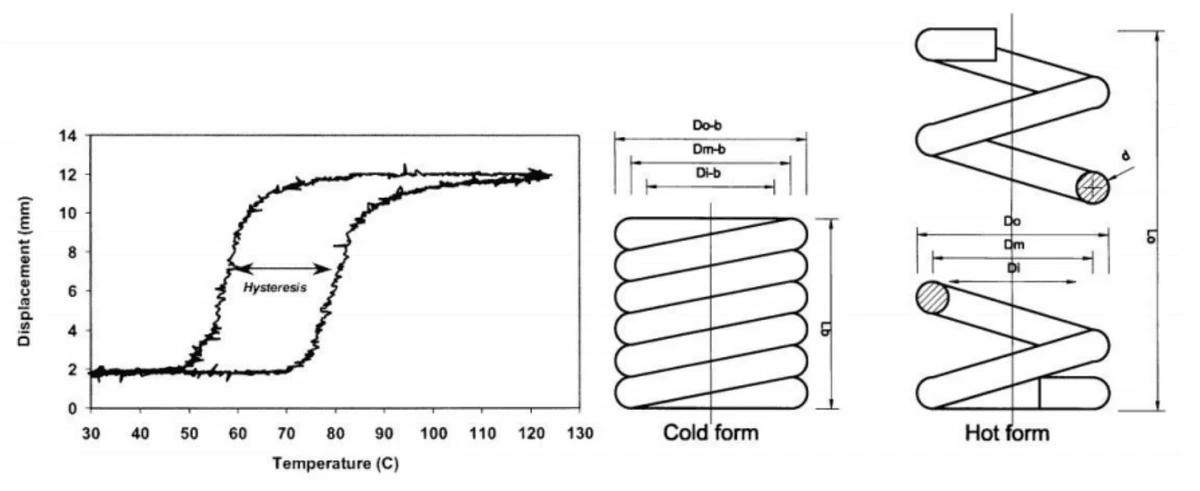
Nitinol springs are not just your average metal coils; they embody a fascinating interplay of physics and material science. To understand how these springs function, we must dive into the principles of shape memory alloys (SMAs) and the unique behaviors exhibited by Nitinol. This section will explore how shape memory works, the phase transformation process, and what makes Nitinol so special in its ability to return to a predetermined shape.
How Shape Memory Works
At its core, the concept of shape memory is all about transformation. A Nitinol spring can be deformed at low temperatures and then return to its original shape when heated above a certain threshold, often referred to as the transformation temperature. This remarkable ability stems from the material's crystalline structure, which allows it to remember its original form.
When you ask, What is a Nitinol spring? it's essential to recognize that this memory effect is what sets it apart from traditional metal springs. The process occurs without any permanent deformation; rather, it’s a reversible change that can be repeated multiple times without degrading performance. Thus, understanding how shape memory works is crucial for harnessing the full potential of Nitinol springs in various applications.
The Phase Transformation Process
The magic behind Nitinol lies in its phase transformation process—specifically between two distinct phases: martensite and austenite. At lower temperatures, Nitinol exists in the martensite phase, which is softer and more easily deformed. When heated above its transition temperature (often around 70°C or 158°F), it transforms into the stronger austenite phase.
This transition isn't just about temperature; it's also about stress and strain within the material. So when we consider What is the temperature of a Nitinol spring? we're really discussing this critical point where functionality kicks in! Understanding this phase transformation helps engineers design systems that leverage these properties effectively while also being aware of potential limitations.
Nitinol's Unique Memory Effect
What truly distinguishes Nitinol from other materials is its unique memory effect—an extraordinary phenomenon allowing it to revert back to an original configuration after deformation. This effect not only applies to springs but also has broader implications for various applications such as medical devices and robotics where precision movement is vital.
However, with great power comes great responsibility; engineers must also consider What are the problems with Nitinol? Despite its advantages like high fatigue resistance and biocompatibility, challenges such as thermal sensitivity can arise if not managed correctly. By appreciating what makes Nitinol so special alongside understanding potential issues, we can better innovate designs that capitalize on this extraordinary alloy's capabilities.
Temperature and Performance
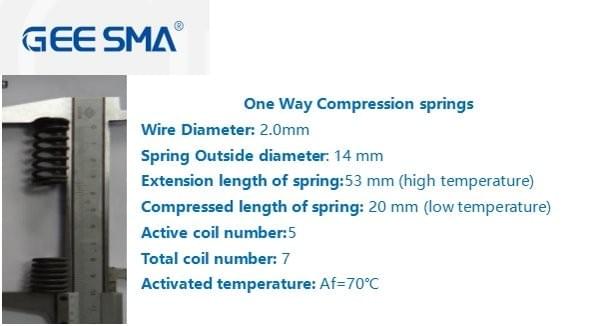
When it comes to Nitinol springs, temperature plays a pivotal role in their functionality and performance. The unique properties of Nitinol, a nickel-titanium alloy, allow these springs to exhibit remarkable shape memory behavior at specific temperatures. Understanding what is the temperature of a Nitinol spring is crucial for optimizing its applications in various industries.
What is the temperature of a Nitinol spring?
The operating temperature of a Nitinol spring can vary widely depending on its specific composition and treatment; typically, it ranges from 0°C to 100°C (32°F to 212°F). However, some specialized variants can operate at even higher temperatures. Knowing how this temperature range correlates with the spring's transformation capabilities is essential for anyone asking, What is Nitinol spring? as it directly affects its performance in practical applications.
Operating Ranges and Limitations
While Nitinol springs are known for their adaptability, they do have operating ranges that must be respected to avoid failure or diminished performance. Exceeding the specified temperature limits can lead to issues such as loss of shape memory effect or even permanent deformation. Additionally, understanding the limitations associated with these materials helps answer common questions about what are the problems with Nitinol? Manufacturers must carefully consider these factors when designing components that utilize this remarkable material.
Impact of Temperature on Functionality
Temperature significantly influences how effectively a Nitinol spring performs its intended function. For instance, if the ambient conditions fluctuate beyond optimal ranges, it may hinder the expected shape recovery process or alter load-bearing capacities. This dynamic interplay between temperature and functionality showcases what is so special about Nitinol: its ability to respond intelligently to environmental changes while maintaining reliability in diverse applications.
Common Challenges with Nitinol
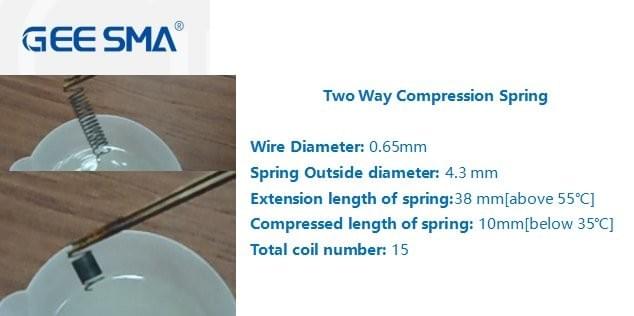
While Nitinol springs have revolutionized various industries with their unique properties, they are not without their challenges. Understanding these issues is crucial for manufacturers and engineers who rely on Nitinol's capabilities. This section delves into the common problems associated with Nitinol springs and explores potential solutions.
What are the problems with Nitinol?
One of the primary concerns regarding Nitinol springs is their susceptibility to various environmental factors that can affect performance. For instance, exposure to extreme temperatures can lead to unexpected behavior in a Nitinol spring, raising questions about reliability in critical applications. Additionally, manufacturing inconsistencies can create variations in the material's properties, leading to unpredictable outcomes when deployed in real-world scenarios.
Another significant challenge is the cost associated with producing high-quality Nitinol components. The intricate processes required for shaping and heat treating these alloys contribute to higher manufacturing expenses compared to traditional materials. Consequently, while many industries recognize what is so special about Nitinol, they must also navigate budget constraints that can limit its widespread adoption.
Lastly, fatigue resistance poses another hurdle for engineers working with Nitinol springs. Repeated cycling through phase transformations can lead to wear over time, potentially causing failure in applications where durability is paramount. Addressing these issues requires a thorough understanding of what makes a Nitinol spring tick and how best to mitigate inherent weaknesses.
Potential Fracture and Fatigue Issues
When discussing potential fractures in a Nitinol spring, it’s essential to consider both mechanical stress and thermal cycling as contributing factors. Mechanical overload can lead to permanent deformation or fracture if the spring exceeds its elastic limits during operation. Furthermore, repeated thermal cycling—where a spring transitions between its martensitic and austenitic phases—can exacerbate fatigue issues over time.
Fatigue failure often occurs after extensive use of a Nitinol spring due to microstructural changes that happen during phase transformations. As these changes accumulate from repeated stress cycles or temperature fluctuations, they may result in cracks forming within the material structure itself. Thus, understanding what is the temperature of a Nitinol spring becomes vital; operating outside recommended ranges increases risks of fractures significantly.
To ensure longevity and reliability of these innovative components, engineers must proactively address potential fatigue issues through careful design considerations and rigorous testing protocols that simulate real-life conditions for their intended applications.
Solutions to Common Nitinol Problems
Addressing common challenges associated with Nitinol springs requires innovative approaches tailored specifically for this unique material. One effective solution involves optimizing manufacturing processes by implementing stringent quality control measures during production stages—ensuring consistent properties across all units produced helps mitigate performance variability due to environmental factors or material inconsistencies.
Another strategy focuses on enhancing fatigue resistance through improved alloy compositions or heat treatment methods designed explicitly for specific applications involving cyclic loading conditions. By fine-tuning these variables based on intended use cases (such as medical devices versus automotive parts), manufacturers can significantly increase durability while maintaining desirable shape memory characteristics inherent in what makes a Nitinol spring so special.
Lastly, ongoing research into advanced coatings or surface treatments may provide additional protection against wear and corrosion—extending service life even further than traditional methods alone could achieve! These combined efforts will help pave the way toward overcoming existing hurdles faced by those utilizing this remarkable alloy technology across diverse fields today.
Unique Features of Nitinol
Nitinol, a fascinating alloy of nickel and titanium, possesses unique features that set it apart from conventional materials. One of the standout attributes is its remarkable ability to return to a predetermined shape when subjected to heat, making Nitinol springs particularly valuable in various applications. This characteristic raises the question: What is so special about Nitinol? The answer lies in its exceptional properties and versatility.
What is so special about Nitinol?
What makes a Nitinol spring truly special is its shape memory effect, which allows it to remember its original form after being deformed. This means that when the temperature rises above a specific threshold, the spring reverts to its pre-deformed shape, showcasing an extraordinary response to thermal changes. Additionally, the superelastic property of Nitinol springs enables them to undergo significant deformation without permanent damage, making them ideal for dynamic applications where flexibility and resilience are paramount.
Advantages Over Traditional Materials
When comparing Nitinol springs with traditional materials like steel or aluminum, several advantages emerge. First and foremost, Nitinol's lightweight nature contributes to overall efficiency in design and manufacturing processes; you get strength without the bulk! Furthermore, unlike conventional springs that may fail under extreme conditions or fatigue over time, Nitinol exhibits remarkable durability and resistance to wear and tear—meaning fewer replacements and lower long-term costs.
Innovation in Design and Engineering
The unique features of Nitinol have spurred innovation across various fields of engineering and design. Manufacturers are now exploring creative uses for these springs beyond traditional applications; from medical devices that adapt dynamically within the human body to robotics where flexibility is essential—Nitinol springs are paving new paths! By integrating this advanced material into their designs, engineers can create more efficient systems that leverage both functionality and aesthetics while addressing common challenges associated with traditional materials.
Conclusion
In conclusion, Nitinol springs are a remarkable innovation in the world of materials science, showcasing versatility that is hard to match. What is Nitinol spring? It’s not just a simple metal; it’s a shape memory alloy that can return to its original shape when heated, making it indispensable in various applications. This unique capability allows for innovative designs in industries ranging from medical devices to automotive engineering.
The Versatility of Nitinol Springs
The versatility of Nitinol springs lies in their ability to adapt and perform under various conditions. What is so special about Nitinol? Its shape memory effect and superelasticity enable these springs to function effectively across a wide temperature range, which leads to enhanced performance in demanding environments. Whether it's used in stents or robotic arms, the applications are as diverse as they are impressive.
GEE SMA’s Role in Advancing Nitinol
GEE SMA has been at the forefront of advancing Nitinol technology, pushing the boundaries of what is possible with this remarkable material. By focusing on innovation and quality, GEE SMA has helped refine the manufacturing processes associated with Nitinol springs and addressed common challenges faced by engineers. They also tackle questions like: What are the problems with Nitinol? By providing solutions that enhance reliability and performance, GEE SMA ensures that customers can fully leverage the advantages of these unique alloys.
Future Outlook for Shape Memory Alloys
Looking ahead, the future outlook for shape memory alloys like Nitinol appears bright and full of potential. As industries continue to explore new applications, understanding what is the temperature of a Nitinol spring will be crucial for optimizing its use across different environments. With ongoing research into overcoming limitations—such as fatigue resistance—Nitinol could become even more integral to technological advancements across various fields.