Introduction
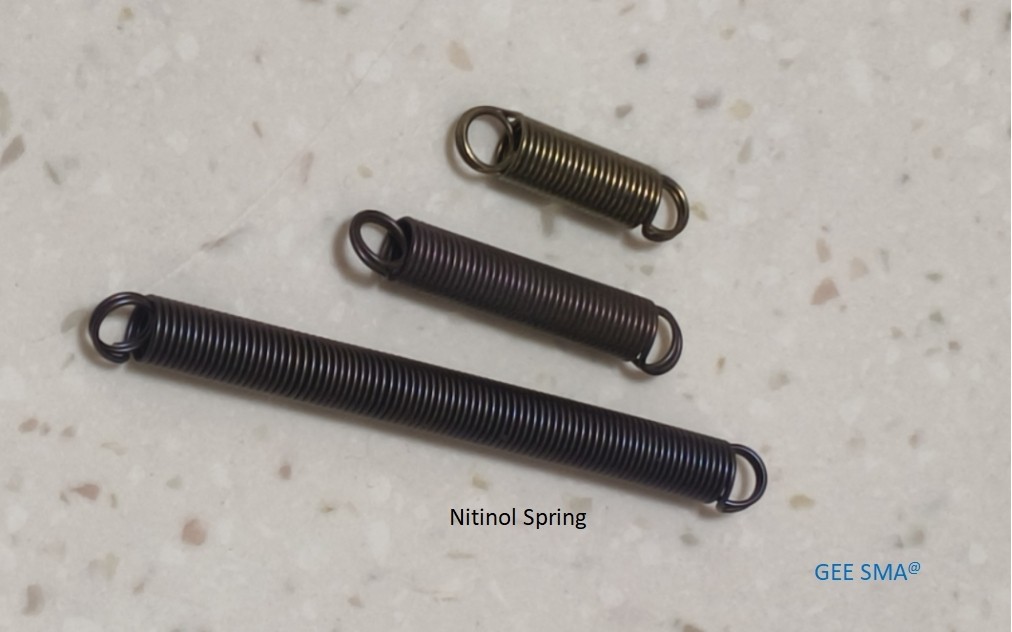
In the world of engineering, few materials possess the enchanting capabilities of shape memory alloys. These remarkable substances can return to their original shape after deformation, a phenomenon that opens up a plethora of innovative design possibilities. Among these alloys, nitinol nickel titanium stands out as a game-changer, particularly in applications requiring precision and resilience.
The Magic of Shape Memory Alloys
Shape memory alloys (SMAs) are not just any ordinary materials; they have an extraordinary ability to remember their original form. This unique characteristic allows them to recover from significant deformations when exposed to certain temperatures or stress levels, making them ideal for applications ranging from aerospace to medical devices. Imagine the potential of a shape memory alloy spring that can adapt and respond dynamically to its environment—it's like having a material with a mind of its own!
Why Design Needs Innovation
In today's fast-paced world, innovation is more than just a buzzword; it's the lifeblood of successful design and engineering solutions. As industries evolve and consumer demands grow ever more complex, designers must seek out advanced materials like nitinol to push boundaries and create products that stand out in the market. The integration of cutting-edge materials such as shape memory alloys not only enhances functionality but also elevates aesthetic appeal and sustainability.
The Role of Nitinol in Engineering
Nitinol nickel titanium is at the forefront of this material revolution, offering unparalleled advantages over traditional spring materials made from steel or other metals. Its unique properties enable engineers to create components that are lighter yet stronger, allowing for more efficient designs without compromising performance. As we delve deeper into the fascinating world of nitinol and its applications—like nitinol foil and specialized nickel springs—we'll uncover how this innovative material is redefining what’s possible in modern engineering.
Understanding Shape Memory Alloys
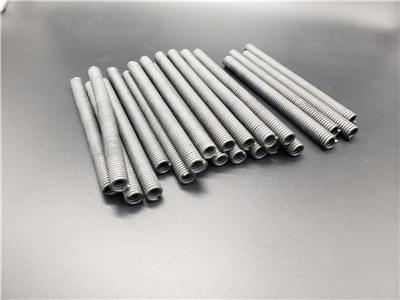
Shape memory alloys (SMAs) are fascinating materials that can return to a predetermined shape when subjected to specific temperatures. One of the most well-known SMAs is nitinol, a nickel-titanium alloy that exhibits remarkable properties, making it a go-to choice for various applications. These unique characteristics enable the creation of innovative designs, particularly in the form of shape memory alloy springs.
What Are Shape Memory Alloys?
Shape memory alloys are metallic materials that can remember their original shape after deformation. When heated above a certain temperature, these alloys revert to their pre-deformed configuration, showcasing an intriguing phenomenon known as the shape memory effect. Nitinol nickel titanium is one of the most popular types of shape memory alloys due to its exceptional strength and flexibility, making it ideal for use in spring material.
These materials are not just limited to niche applications; they have found their way into everyday products and advanced technologies alike. From medical devices like stents and guidewires to aerospace components requiring lightweight yet durable solutions, the versatility of SMAs is impressive. The unique properties offered by nitinol allow engineers and designers to push boundaries in innovation while ensuring reliability and performance.
The Science Behind Shape Memory
The science behind shape memory alloys revolves around phase transformations between two distinct crystalline structures: martensite and austenite. At lower temperatures, nitinol exists in the martensitic phase, which is more malleable and can be easily deformed into various shapes—ideal for creating custom spring configurations. Upon heating above its transformation temperature, it transitions into the austenitic phase where it regains its original form with considerable force.
This transition occurs due to changes in atomic arrangements within the material's structure when heat is applied or removed. The ability of nitinol nickel titanium to undergo such transformations makes it an excellent candidate for applications requiring precise movement or actuation—features often desired in medical devices or aerospace engineering designs. Understanding this underlying science allows engineers to harness these properties effectively when designing products utilizing shape memory alloy springs.
Applications of Shape Memory Alloys
The applications of shape memory alloys are vast and varied across multiple industries due to their unique capabilities. In medicine, nitinol is commonly used for stents that expand within arteries upon reaching body temperature—an essential function for improving blood flow without invasive procedures. Additionally, these innovative materials have found uses in robotics where actuators made from nitinol foil enable precise movements with minimal energy consumption.
In aerospace engineering, lightweight yet strong components made from nickel spring technology contribute significantly to fuel efficiency while maintaining structural integrity during flight conditions. Automotive manufacturers also capitalize on SMAs for systems like self-adjusting seat belts or adaptive suspension systems that enhance passenger comfort and safety on varying terrains. With such diverse applications emerging regularly, it's clear that shape memory alloys will continue revolutionizing design across numerous sectors well into the future.
The Unique Properties of Nitinol
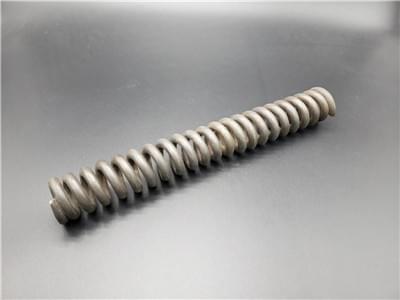
Nitinol, a unique alloy composed primarily of nickel and titanium, boasts remarkable properties that set it apart in the realm of engineering materials. Known for its shape memory effect and superelasticity, this nickel material can return to a predetermined shape when heated, making it an exceptional choice for various applications. The combination of these characteristics allows nitinol to excel as a shape memory alloy spring, providing innovative solutions across multiple industries.
Characteristics of Nitinol Nickel Titanium
Nitinol nickel titanium is celebrated for its extraordinary mechanical properties, which include high flexibility and resilience. This means that when subjected to stress or deformation, nitinol can undergo significant changes while still maintaining its structural integrity. Additionally, the unique phase transformation between its austenite and martensite states enables this shape memory alloy to perform in extreme conditions without compromising performance.
Another fascinating characteristic of nitinol is its biocompatibility, making it an ideal candidate for medical applications such as stents and guidewires. Its ability to adapt under varying temperatures also positions it favorably against traditional spring materials like steel or plastic. With properties like these, it's no wonder that nitinol is rapidly becoming the go-to choice for engineers looking for cutting-edge solutions.
Advantages of Using Nitinol for Springs
One major advantage of using nitinol for springs is its ability to recover from deformation without permanent change – a feature not commonly found in conventional spring materials. This means that a nitinol spring can be compressed or stretched multiple times while returning reliably to its original form after each cycle. Such durability not only enhances product longevity but also reduces maintenance costs over time.
Furthermore, the lightweight nature of nitinol makes it particularly advantageous in aerospace and automotive applications where reducing weight is critical without sacrificing strength or functionality. By incorporating shape memory alloy springs into designs, engineers can create more efficient systems that take full advantage of this remarkable material's properties. This leads to innovations that are both practical and sustainable.
Lastly, the versatility offered by nitinol foil allows designers to explore new forms and shapes that were previously unachievable with traditional materials. Whether it's creating complex geometries or integrating smart features into products, the use of nitinol opens up endless possibilities for innovation across various sectors.
Comparing Nitinol with Other Materials
When comparing nitinol with other materials commonly used in spring manufacturing—such as stainless steel or carbon fiber—the advantages become glaringly obvious. While traditional nickel springs may exhibit good tensile strength, they often lack the unique properties offered by shape memory alloys like nitinol; notably their ability to remember shapes under thermal influence. This distinct capability gives design engineers an edge when developing products requiring precision movement and adaptability.
Moreover, unlike many conventional metals that can corrode over time under harsh conditions, nitinol's inherent resistance to oxidation ensures longevity even in challenging environments—making it a superior choice for critical applications across industries such as aerospace and medicine where reliability is paramount.
In summary, while there are many options available within the realm of spring material choices today—from classic metals like steel to advanced composites—the unmatched qualities found in nitinol nickel titanium make it stand out from the crowd as an innovative solution worth considering.
Revolutionizing Design with Shape Memory Alloy Springs
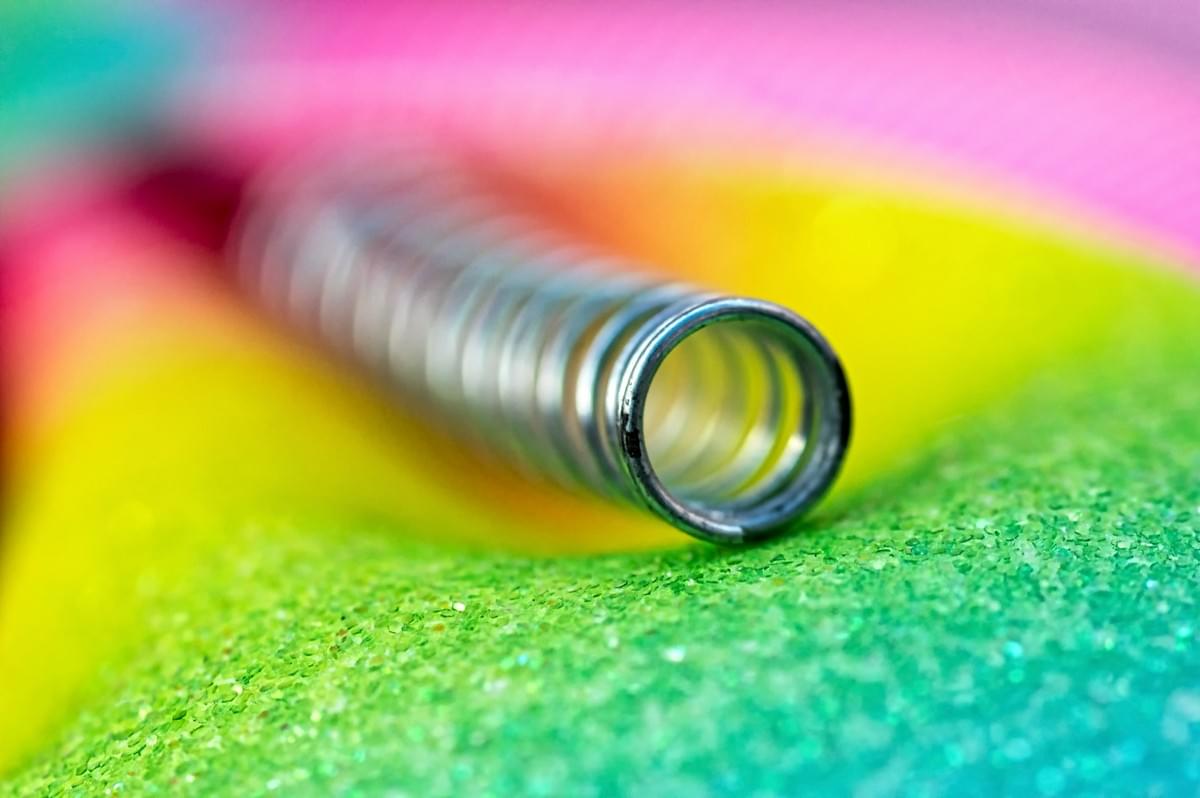
Shape memory alloy springs, particularly those made from nitinol nickel titanium, are transforming various industries by providing unique solutions that were previously unattainable. These innovative springs can return to their original shape after deformation, making them invaluable in applications requiring precision and reliability. As we explore the impact of these remarkable materials, it becomes clear that their versatility is reshaping engineering paradigms across multiple sectors.
Transforming Aerospace Engineering
In aerospace engineering, the demands for lightweight and durable materials are paramount, and shape memory alloy springs fit the bill perfectly. Nitinol's ability to recover its shape under stress allows for more efficient designs in aircraft components and systems. By integrating nitinol nickel titanium into critical applications like actuators and control surfaces, engineers are enhancing performance while reducing overall weight—an essential factor in modern aviation.
The use of these nickel spring materials improves not only functionality but also safety in aerospace applications. For instance, a shape memory alloy spring can respond dynamically to environmental changes or mechanical stress without compromising structural integrity. This adaptability leads to innovations such as morphing wings that adjust during flight for optimal aerodynamics.
Moreover, with advancements in nitinol foil technology, manufacturers can create thinner components without sacrificing strength or performance. This opens up new possibilities for designing complex systems that require intricate movements while remaining lightweight—a crucial aspect in the competitive field of aerospace engineering.
Innovations in Medical Devices
The medical field has experienced a revolution thanks to the incorporation of shape memory alloy springs into device design. Nitinol's biocompatibility makes it an ideal choice for various medical applications, including stents and surgical instruments that require precise manipulation within the human body. The unique properties of nitinol nickel titanium allow these devices to expand or contract at body temperature, offering tailored solutions for patient care.
One significant advantage of using shape memory alloys is their ability to minimize invasiveness during procedures. For example, a nitinol spring can be compressed for easy insertion into the body and then deployed into its original form once positioned correctly—reducing recovery time and improving patient outcomes significantly. This innovation exemplifies how incorporating advanced materials like nitinol can lead to better healthcare solutions.
Additionally, ongoing research continues to unveil new uses for nitinol foil within medical devices—from catheters that navigate complex pathways with ease to orthopedic implants designed for optimal healing outcomes. As designers embrace these advancements in spring material technology, patients benefit from safer procedures with enhanced efficacy.
Enhancements in Automotive Applications
The automotive industry is also reaping the rewards of integrating shape memory alloy springs into vehicle design and manufacturing processes. With rising demands for fuel efficiency and performance enhancements, using materials like nitinol nickel titanium allows engineers to develop lighter yet robust components without compromising safety standards or functionality. The unique properties of these alloys enable innovative features such as automatic seat adjustments or adaptive suspension systems that respond intelligently to driving conditions.
Nitinol's remarkable characteristics make it an excellent choice for various automotive applications beyond just springs; its flexibility allows manufacturers to create intricate designs tailored specifically for modern vehicles' needs while maintaining high levels of durability over time. Moreover, employing nickel spring technologies contributes significantly toward achieving sustainable design goals by reducing overall vehicle weight—thereby improving fuel efficiency.
As car manufacturers continue exploring new opportunities presented by shape memory alloys like nitinol foil within their designs—the future looks promising! From advanced engine components capable of adjusting based on temperature changes to smart locking mechanisms enhancing security features—innovation knows no bounds when leveraging this groundbreaking material.
GEE SMA: Pioneers in Nitinol Technology
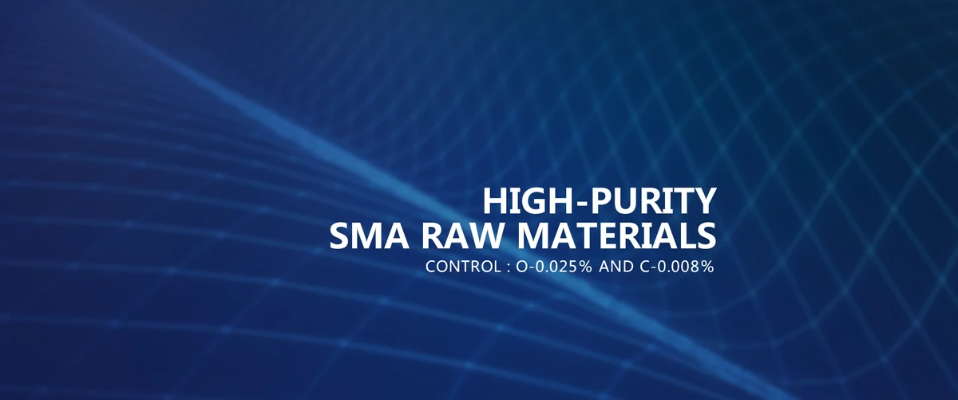
When it comes to shape memory alloys, GEE SMA stands out as a beacon of innovation and expertise. This company has carved a niche in the market, focusing specifically on nitinol nickel titanium, a remarkable material that revolutionizes various industries. Their commitment to pushing the boundaries of what’s possible with shape memory alloy springs makes them a leader in this field.
Overview of GEE SMA's Expertise
GEE SMA specializes in the development and manufacturing of advanced nitinol products, particularly shape memory alloy springs that exhibit incredible mechanical properties. The team at GEE SMA is composed of material scientists and engineers who understand the intricacies of nickel materials and their applications in real-world scenarios. Their deep knowledge allows them to create tailored solutions that meet specific client needs, ensuring optimal performance from every piece they produce.
Custom Solutions for Diverse Industries
One of the standout features of GEE SMA is their ability to deliver custom solutions across various sectors, from aerospace to medical devices. They understand that each application may require unique specifications, whether it’s a highly specialized nickel spring or intricate nitinol foil configurations. By leveraging their expertise in shape memory alloys, they can design products that not only meet but exceed industry standards while also enhancing functionality and reliability.
Commitment to Quality and Innovation
At GEE SMA, quality isn’t just a buzzword; it’s woven into the fabric of their operations. They adhere to rigorous testing protocols for all their shape memory alloy springs and other nitinol products, ensuring durability and performance under varying conditions. Coupled with an unwavering commitment to innovation, GEE SMA continuously explores new technologies and methodologies that keep them at the forefront of the nitinol market.
Future Trends for Shape Memory Alloys
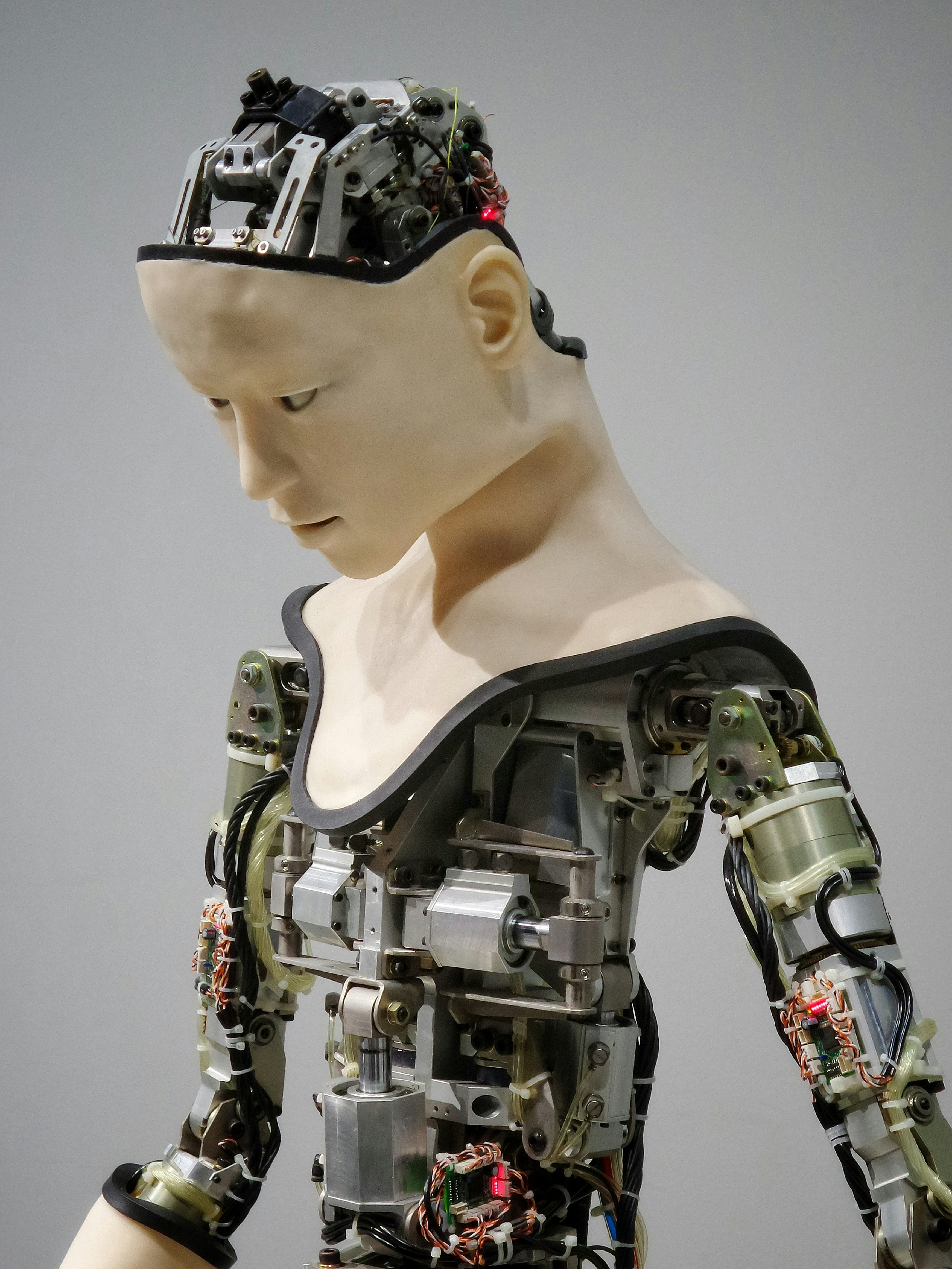
The future of shape memory alloys (SMAs) is bright, with innovative applications emerging across various sectors. As industries continue to explore the unique properties of materials like nitinol nickel titanium, the potential for new designs and functionalities becomes limitless. From robotics to consumer goods, the versatility of shape memory alloy springs will play a pivotal role in shaping tomorrow's technology.
Emerging Applications in Robotics
Robotics is on the brink of a revolution thanks to the integration of shape memory alloy springs. These springs, made from nitinol nickel titanium, offer remarkable flexibility and adaptability that traditional materials simply can't match. As robotic systems become more complex and require precise movements, SMAs will enable engineers to design lighter, more efficient robots that can perform intricate tasks with ease.
In particular, the use of shape memory alloys in actuators promises to enhance robotic dexterity significantly. Imagine a robot that can morph its structure or grip objects with varying strengths—this is not just science fiction; it’s becoming reality with nitinol technology! The ability to create compact mechanisms using nickel spring configurations allows for innovative designs that were previously unimaginable.
Furthermore, as industries push towards automation and smart technologies, the demand for advanced robotics will only increase. This trend will further drive research into new applications for SMAs in robotics, ensuring that nitinol remains at the forefront of engineering innovation.
Integrating Shape Memory Alloys in Consumer Goods
The consumer goods market is beginning to embrace shape memory alloys like never before. From fashion accessories that change shapes based on temperature to home gadgets that adapt their functionality according to user needs, nitinol nickel titanium is paving the way for smarter products. This adaptability makes SMAs an attractive choice for designers looking to create unique experiences for consumers.
Imagine a jacket made from fabric embedded with shape memory alloy springs; it could adjust its fit based on body temperature or activity level! Such innovations not only enhance comfort but also add an element of excitement and novelty to everyday items. With consumers increasingly seeking personalized experiences, integrating SMAs into products could be a game-changer.
Moreover, as sustainability becomes a critical concern among consumers and manufacturers alike, using durable materials like nitinol foil presents an eco-friendly solution. These materials are not only long-lasting but also reduce waste by minimizing wear-and-tear over time—appealing factors in today’s market landscape focused on sustainability.
The Growing Market for Nitinol Foil and Springs
The demand for nitinol foil and springs is expected to surge as industries recognize their advantages over traditional spring materials. With their unique properties such as superelasticity and thermal responsiveness, these shape memory alloy components are becoming indispensable across various applications—from medical devices to aerospace engineering innovations. As companies invest in research and development focused on these materials, we can anticipate even more groundbreaking uses emerging soon.
Additionally, manufacturers are exploring opportunities within niche markets where specialized performance characteristics are required—areas where standard nickel material falls short. For example, customized solutions utilizing nitinol allow engineers to design components tailored specifically for challenging environments or demanding applications without compromising quality or performance standards.
With this growing interest comes an expanding marketplace dedicated solely to SMAs like nitinol springs and foils—creating opportunities not just for manufacturers but also for entrepreneurs looking at novel applications across diverse sectors! As we move forward into this exciting era driven by innovation and creativity surrounding shape memory alloys; one thing is clear: they’re here to stay!
Conclusion
The journey through the world of shape memory alloys, particularly focusing on nitinol nickel titanium, reveals a transformative potential in engineering and design. These materials redefine traditional concepts by introducing capabilities that were once the realm of science fiction. As industries evolve, the integration of shape memory alloy springs will undoubtedly reshape how we approach problem-solving across various sectors.
Redefining Engineering with Shape Memory Alloys
Shape memory alloys (SMAs) like nitinol nickel titanium are revolutionizing engineering paradigms by offering unique functionalities that standard materials simply cannot match. The ability of these materials to return to a predetermined shape when heated opens new avenues for innovation in design and function. Engineers are now able to create solutions that are not only efficient but also adaptable, leading to designs that can respond dynamically to their environments.
The Competitive Edge of Nitinol Springs
When it comes to spring material, nitinol springs stand out due to their remarkable properties such as superelasticity and high fatigue resistance. These characteristics give nitinol springs a competitive edge over traditional nickel spring options, making them ideal for demanding applications where reliability is critical. Furthermore, the lightweight nature of nitinol foil enhances its appeal in industries like aerospace and automotive, where every gram counts towards efficiency.
Embracing Innovation for Future Designs
Looking ahead, embracing innovation through the use of shape memory alloy springs will be pivotal for future designs across multiple sectors. The ongoing research into new applications for nitinol nickel titanium promises exciting developments in robotics and consumer goods alike. By harnessing the unique properties of SMAs today, we set the stage for groundbreaking advancements that will define tomorrow's engineering landscape.