Introduction
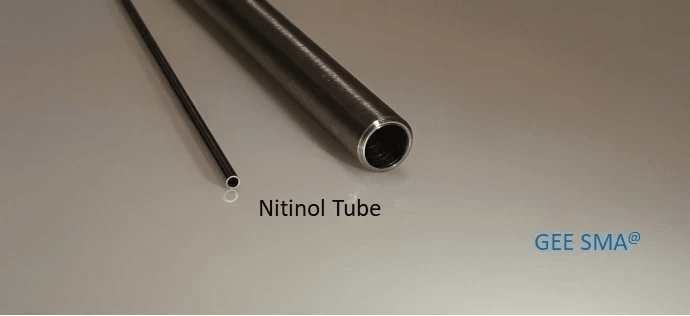
In the realm of medical manufacturing, few materials have garnered as much attention and acclaim as Nitinol. This unique alloy, a combination of nickel and titanium, exhibits remarkable properties that make it a game-changer in various medical applications. From stents to guidewires, understanding Nitinol's capabilities is essential for harnessing its full potential in the healthcare sector.
Understanding Nitinol in Medical Manufacturing
Nitinol products are not just any ordinary materials; they possess extraordinary qualities such as superelasticity and shape memory, which are crucial for many medical devices. The ability of Nitinol to return to its original shape after deformation is particularly useful in applications requiring flexibility and resilience, such as Nitinol tubes and rods used in minimally invasive surgeries. Moreover, the biocompatibility of Nitinol makes it an ideal choice for implants and surgical instruments that interact with human tissues.
The Importance of Customized Nitinol Products
Tailored solutions like Nitinol sheets and strips can be designed to meet precise specifications required by healthcare providers or device manufacturers. By offering customized options such as different thicknesses or treatments for Nitinol foil, manufacturers can enhance performance while addressing unique operational challenges faced by medical professionals.
GEE SMA: Leaders in Nitinol Solutions
When it comes to expertise in producing high-quality Nitinol products, GEE SMA stands out as a leader in the industry. Their commitment to innovation ensures that they provide an extensive range of customized solutions including Nitinol wire and springs tailored for various applications within the medical field. Partnering with GEE SMA means accessing not only superior products but also a wealth of knowledge on how best to utilize these advanced materials for improved patient outcomes.
Key Benefits of Nitinol Products
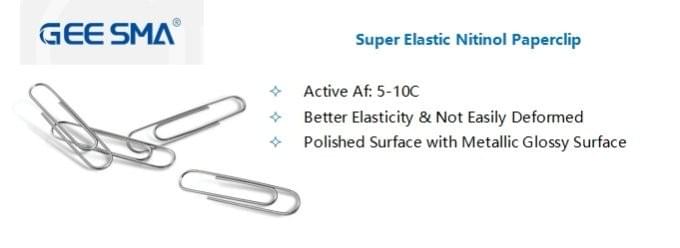
Nitinol products are revolutionizing the medical manufacturing landscape with their unique properties, versatility, and significant contributions to patient outcomes. As a shape memory alloy that can return to its original form after deformation, Nitinol is making waves across various medical fields. From Nitinol Sheet to Nitinol Spring, these products offer unparalleled advantages that cater to the specific demands of healthcare professionals.
Unique Properties of Nitinol
One of the standout features of Nitinol products is their remarkable shape memory and superelasticity. This means that when a Nitinol Tube or Rod is subjected to stress, it can revert back to its preset shape upon heating or unloading, making it ideal for intricate medical applications. Additionally, the biocompatibility of Nitinol ensures minimal adverse reactions when implanted in the human body, enhancing its appeal in surgical settings.
Moreover, the ability to manufacture customized forms such as Nitinol Foil and Wire allows engineers and designers to create tailored solutions for specific challenges in medicine. Whether it's crafting a precise stent or developing specialized surgical instruments, these unique properties make Nitinol an essential material in modern healthcare innovations. The versatility inherent in this alloy is not just a bonus; it's a game-changer.
Versatility in Medical Applications
The versatility of Nitinol products extends far beyond traditional uses; they are now integral components across numerous medical applications. From cardiovascular devices like stents made from Nitinol Strip to orthopedic implants utilizing robust Nitinol Rods, this material adapts seamlessly to various environments and requirements. Its lightweight yet durable nature makes it an optimal choice for everything from minimally invasive surgical tools to complex robotic systems.
Furthermore, manufacturers are increasingly exploring new ways to leverage the properties of Nitinol Foil and Wire for innovative applications such as guidewires and catheters. The adaptability of these materials allows them not only to perform effectively but also enhances operational efficiency during procedures—an invaluable asset for surgeons striving for precision and speed. The ongoing research into additional applications continues to unveil exciting possibilities within the realm of medical technology.
Enhanced Patient Outcomes
Ultimately, one of the most compelling reasons for embracing customized Nitinol products lies in their ability to enhance patient outcomes significantly. By utilizing advanced materials like Nitinol Spring or Tube in device design, healthcare providers can improve treatment efficacy while minimizing complications associated with traditional materials. Patients benefit from reduced recovery times due to less invasive procedures made possible by these innovative designs.
Moreover, because many devices made from nitinol are designed with flexibility and resilience in mind, they often result in fewer post-operative issues compared with conventional options—leading directly toward better long-term health results for patients undergoing various treatments. The continuous evolution and refinement of nitinol technologies promise even more advancements that could further improve care delivery across diverse patient populations.
Types of Nitinol Products
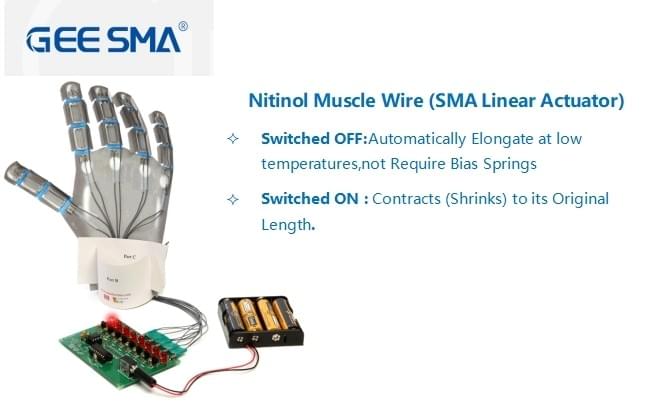
Nitinol products come in various forms, each tailored to meet specific needs in medical applications. Understanding the differences among Nitinol Sheet, Nitinol Strip, Nitinol Foil, Nitinol Tube, Nitinol Rod, Nitinol Wire, and Nitinol Spring can help manufacturers and healthcare providers select the best option for their requirements. Let's dive into these versatile forms of nitinol and explore their unique characteristics.
Exploring Nitinol Sheet and Strip
Nitinol Sheet and Strip are essential components in the realm of nitinol products due to their unique properties and adaptability. These flat forms can be easily cut or shaped for a variety of medical applications, including stents and orthopedic devices. The ability to customize the thickness and dimensions allows manufacturers to create solutions that fit precise specifications while maintaining the inherent benefits of nitinol's shape memory effect.
The flexibility of Nitinol Sheet makes it ideal for applications requiring a combination of strength and ductility. Whether used in minimally invasive procedures or as part of larger assemblies, these sheets offer significant advantages over traditional materials like stainless steel or titanium. Moreover, the lightweight nature of nitinol contributes to improved patient comfort during recovery.
The Role of Nitinol Foil
Nitinol Foil is another fascinating form within the family of nitinol products that deserves attention for its thinness and exceptional performance characteristics. Often utilized in specialized applications such as sensors or actuators, this ultra-thin material allows for intricate designs that can respond dynamically to temperature changes or mechanical stress. Its lightweight profile makes it particularly advantageous in situations where every gram counts.
In addition to its practical uses, Nitinol Foil also plays a vital role in advancing technology within medical devices. By integrating foil into devices like guidewires or catheter systems, manufacturers can enhance functionality without compromising on performance metrics such as flexibility or resilience. This versatility is what sets nitinol apart from other materials.
Utilizing Nitinol Tube and Rod
These cylindrical forms are often employed in stents or implants where a robust yet flexible solution is required—perfectly illustrating why customization is key in this sector. Their unique ability to return to a predetermined shape after deformation makes them indispensable tools for surgeons.
Nitinol Tubes are particularly beneficial when designing devices that require expansion within the body after being inserted through small incisions—think angioplasty balloons! Meanwhile, Niton Rods offer excellent tensile strength while remaining lightweight enough not to add unnecessary burden during procedures. Together they pave the way toward innovative solutions that prioritize patient safety without sacrificing effectiveness.
Advantages of Niton Wire and Spring
Last but certainly not least are two more remarkable members of our list: Niton Wire and Spring—both pivotal components among nitinol products known for their elasticity and durability under stress conditions! The use cases here span from dental tools that require precision movement all the way through orthopedic springs designed specifically for joint replacements—a testament to how versatile these materials truly are!
One major advantage lies within their inherent ability as shape memory alloys; both wire & spring configurations can adapt dynamically based on temperature fluctuations—allowing them not only functionally but also aesthetically appealing options across diverse fields! Furthermore, thanks largely due its corrosion resistance properties which enhances longevity—making them reliable choices across numerous applications over time!
Customization Processes in Nitinol Manufacturing
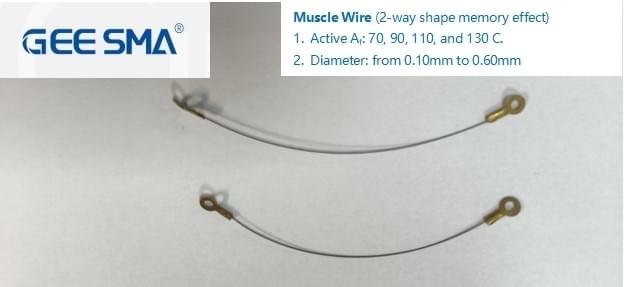
Customization in Nitinol manufacturing is essential for creating products that perfectly fit specific medical applications. By tailoring designs to meet the unique demands of healthcare professionals, manufacturers can ensure that their nitinol products deliver optimal performance and reliability. This process not only enhances functionality but also contributes to improved patient outcomes.
Tailoring Designs for Specific Applications
The versatility of materials like Nitinol Sheet and Nitinol Strip allows manufacturers to create customized solutions tailored to particular surgical procedures or medical devices. For instance, a specialized Nitinol Tube may be designed with varying diameters and wall thicknesses to meet the precise requirements of a catheter, ensuring its effectiveness during use.
Moreover, customization extends beyond dimensions; it also encompasses the mechanical properties of the material itself. By adjusting the composition or treatment processes, manufacturers can produce Nitinol Wire and Nitinol Spring with specific shape memory characteristics or stiffness levels suitable for different applications. This level of personalization ensures that each product meets rigorous industry standards and addresses real-world challenges faced by medical professionals.
Advanced Techniques for Precision Manufacturing
Precision is paramount in the production of nitinol products, which is why advanced manufacturing techniques are employed throughout the process. Techniques such as laser cutting and CNC machining allow for incredibly accurate shaping of materials like Nitinol Foil and Nitinol Rod, resulting in components that fit seamlessly into devices or instruments without compromising quality. These methods also facilitate intricate designs that enhance functionality while maintaining structural integrity.
Additionally, additive manufacturing has emerged as a game-changer in producing customized nitinol products. This technology enables the creation of complex geometries that were previously impossible with traditional methods, allowing for innovative designs in surgical instruments or implants made from nitinol materials. Such advancements signify a leap forward in precision manufacturing, ensuring each application can leverage the unique properties of nitinol effectively.
Collaborating with GEE SMA for Unique Needs
With their extensive experience in working with various forms such as Nitinol Wire and Nitinol Spring, GEE SMA can help you navigate through design considerations while providing insights into material selection based on your project requirements. Their collaborative approach ensures that your vision transforms into reality while adhering to strict quality standards.
Moreover, GEE SMA’s commitment to innovation means they are always exploring new techniques and technologies to enhance their offerings further. Whether you require specialized dimensions for a particular application using Nitinol Sheet or need assistance developing custom solutions from scratch using Nitinol Tube or Rod, their team is dedicated to delivering exceptional results tailored just for you. With GEE SMA by your side, you’ll have access not only to high-quality materials but also expertise that drives success across all stages of development.
Quality Assurance in Nitinol Production
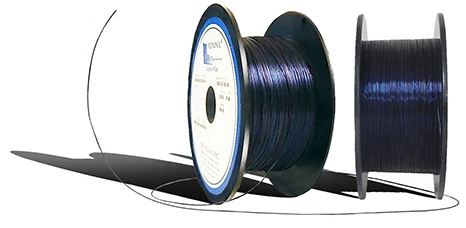
Importance of Quality Control
Quality control in nitinol production involves rigorous testing and inspection processes to guarantee that all nitinol products meet specified criteria. From the initial sourcing of raw materials to the final inspection of Nitinol Rods and Nitinol Wires, every step is crucial for maintaining high-quality outputs. A failure at any stage could lead to compromised performance in critical applications like surgical instruments or implants.
Moreover, consistent quality control fosters trust between manufacturers and healthcare providers. When hospitals and clinics know they can rely on high-quality Nitinol Springs or Foils from a supplier, they are more likely to choose those products for their patients' needs. Ultimately, robust quality assurance translates into better healthcare outcomes.
Certifications and Standards to Consider
When evaluating nitinol products for medical use, various certifications and industry standards come into play. Organizations such as ISO (International Organization for Standardization) set forth guidelines that ensure manufacturers maintain high levels of quality across their product lines—including Nitinol Sheets and Strips. Compliance with these standards not only ensures product reliability but also demonstrates a commitment to excellence in manufacturing practices.
Additionally, certifications specific to medical devices—like FDA approval—are critical when considering the use of customized nitinol products in sensitive applications like cardiovascular stents or orthopedic implants. These certifications serve as a badge of honor for companies like GEE SMA that prioritize safety and efficacy above all else.
GEE SMA's Commitment to Excellence
At GEE SMA, our dedication to excellence is reflected in every aspect of our production process for nitinol products. We employ advanced quality control measures that include thorough inspections at various stages—from raw material selection through final product testing—ensuring each Nitinol Tube or Wire meets our stringent specifications before reaching clients' hands. Our commitment extends beyond compliance; we strive for continuous improvement through innovation in both manufacturing techniques and product development.
Furthermore, we actively seek feedback from our partners in the medical field to enhance our offerings continually. By collaborating closely with healthcare providers who utilize our customized nitinol solutions—whether it's a specialized Nitinol Spring or an intricate Nitinol Foil—we can adapt our processes based on real-world needs and challenges faced by practitioners today.
In conclusion, GEE SMA stands firm as a leader not just because we produce exceptional nitinol products but also due to our unwavering commitment to maintaining high-quality standards throughout every step of production.
Real-World Applications of Customized Nitinol
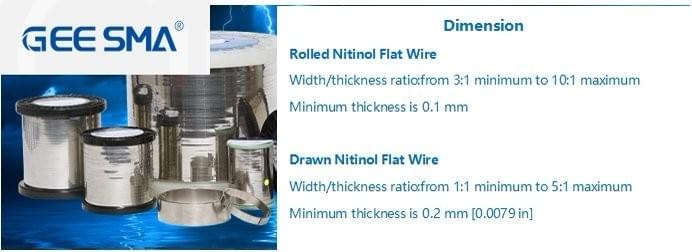
The versatility of customized nitinol products is showcased in various real-world applications, particularly in the medical field. From innovative devices to surgical instruments, nitinol's unique properties are revolutionizing patient care and outcomes. This section explores case studies, groundbreaking innovations, and future trends associated with nitinol utilization.
Case Studies in Medical Devices
Customized nitinol products have made significant strides in medical devices over the past few years. For instance, the use of Nitinol Sheet and Nitinol Strip in stent designs has led to improved flexibility and biocompatibility, allowing for better integration within the human body. One case study highlighted a cardiac stent that utilized Nitinol Wire for its shape memory effect, enhancing its ability to expand upon deployment while minimizing complications.
Another notable example comes from orthopedic implants that incorporate Nitinol Rods and Tubes for their strength-to-weight ratio. These implants have demonstrated remarkable performance in load-bearing applications while reducing recovery times for patients. Moreover, a recent study showed how customized Nitinol Foil is used in drug delivery systems to ensure precise medication release profiles tailored to individual patient needs.
Innovations in Surgical Instruments
The realm of surgical instruments has also greatly benefited from advancements in customized nitinol products. Surgeons are now using tools made from Nitinol Wire and Springs that offer enhanced flexibility during minimally invasive procedures. These instruments can bend without breaking, allowing surgeons to navigate complex anatomical structures with ease.
Additionally, innovations such as self-expanding vascular access devices made from Nitinol Tube are transforming how procedures are performed. Their ability to adapt to varying vessel sizes ensures a secure fit while minimizing trauma during insertion. With the integration of Nitinol Foil into scalpel designs, surgical precision has reached new heights—offering sharper edges that maintain their integrity throughout multiple uses.
Future Trends in Nitinol Utilization
Looking ahead, the future of nitinol utilization appears promising as research continues into its unique properties and potential applications across various fields beyond medicine. The ongoing development of smart medical devices incorporating sensors made from customized Nitinol Sheet could revolutionize patient monitoring by providing real-time data on vital signs or implant performance.
Moreover, advancements in manufacturing techniques will likely lead to even more intricate designs using materials like Nitinol Strip and Wire for next-generation prosthetics that mimic natural movement more closely than ever before. As industries embrace customization further, we can expect an influx of innovative solutions derived from nitinol products—paving the way for enhanced healthcare solutions tailored specifically to individual needs.
Conclusion
In the ever-evolving landscape of medical manufacturing, customization emerges as a pivotal factor in delivering superior solutions. By embracing tailored designs, manufacturers can optimize the performance of nitinol products, ensuring they meet specific patient needs and clinical requirements. Whether it’s Nitinol Sheet, Nitinol Strip, or more complex forms like Nitinol Tube and Rod, customization translates to enhanced efficacy and improved patient outcomes.
Embracing Customization for Better Solutions
The journey towards better healthcare solutions begins with recognizing that one size does not fit all. Customized nitinol products such as Nitinol Foil and Nitinol Wire allow for innovative designs that cater to unique medical applications. This level of personalization not only enhances functionality but also fosters a deeper connection between technology and patient care.
Moreover, the versatility of nitinol materials means that each product can be designed with specific properties in mind—be it flexibility from Nitinol Spring or strength from Nitinol Rods. This adaptability is crucial in developing advanced medical devices that respond effectively to diverse clinical challenges. As we move forward, embracing these customized solutions will undoubtedly pave the way for breakthroughs in medical technology.
The Future of Nitinol in Medicine
Looking ahead, the future of nitinol products appears bright and brimming with potential. With ongoing advancements in material science and manufacturing techniques, we can expect even more innovative applications for nitinol materials like Nitinol Sheet and Strip across various medical fields. From minimally invasive surgical instruments to groundbreaking implant technologies, the possibilities seem limitless.
As healthcare continues to prioritize patient-centered approaches, nitinol’s unique properties will play an increasingly vital role in shaping effective treatments. The combination of shape memory effects and biocompatibility positions nitinol products at the forefront of next-generation medical devices—making them indispensable tools for clinicians worldwide. In this dynamic environment, staying attuned to emerging trends will ensure that manufacturers remain competitive while meeting evolving healthcare demands.
Partnering with GEE SMA for Success
To harness the full potential of customized nitinol products, collaboration is key—especially when partnering with industry leaders like GEE SMA. Their expertise in producing high-quality materials such as Nitinol Foil and Wire ensures that clients receive tailored solutions perfectly aligned with their specifications. GEE SMA's commitment to innovation alongside rigorous quality assurance processes guarantees excellence at every stage of production.
Moreover, by working closely with GEE SMA's skilled team during design phases, clients can tap into advanced techniques that enhance precision manufacturing capabilities across all types of nitinol products—from tubes to springs. This partnership not only streamlines development but also fosters an environment where creativity meets functionality head-on—ultimately leading to successful outcomes for both manufacturers and patients alike.
In conclusion, as we embrace customization within the realm of nitinol manufacturing, we set ourselves on a path toward groundbreaking advancements in medicine that prioritize patient well-being above all else.